Before reading the below examples, please be aware, FlySeer™ is a platform for creating a set of Rules and Alerts for whatever aircraft condition you want to be aware of. It may be airspeed, pitch, bank, height above ground, gear up/down, or anything else that can be measured. The examples below are Rules and Alerts we’ve thought about and are currently testing. If there’s something else you want to know about, please Contact Us, and we’ll help you create it. We do imagine that over time, type clubs or organizations will want to build a shared library of Rules and Alerts, and we’re working to make that happen.
We are starting with GPS or Tablet/Smartphone based alerts, but we plan to add devices to the Flight-Coach platform such as cameras, current sensors, position sensors and more, to be able to interact with all your aircraft instruments and systems over time.
SAFETY WARNING SYSTEM SUCH AS GEAR ALERTING – VIRTUAL CO-PILOT
We started out thinking about the problem of landing a retractable
gear aircraft without putting the gear down as one of the most common general
aviation safety issues. Pilots tend to
make mistakes when they are distracted.
Distractions can come from anywhere, examples include Air Traffic
Control, Traffic, Birds, Weather, Passengers, etc. It’s the
nightmare that every retractable-gear pilot fears: A perfect flight, followed
by a belly flop on the runway because someone forgot or was distracted by a
minor event in the cockpit to lower the landing gear.
This scenario happens to pilots with a wide
range of experience. According to the NTSB, more than half of
all reported landing gear related incidents are unintentional
gear-up landings. Industry experts forecast that 30+ pilots will land gear up
this year…or about one every 12 days! When they happen, insurance
costs can be from a low in the $50,000 range, up to the millions.
Typical general aviation aircraft equipped with retractable gear have no warning system to alert the pilot when to put the gear down. They typically have 1 to 3 green lights to indicate that the gear is down and locked and a yellow or red light to indicate the gear is up or in transit. Those factory systems that do have an alert, such as the Piper Arrow aircraft, typically operate by sounding an alert when the airspeed is below a factory set value and the power is reduced below a factory set value. These systems are far from ideal, and are often over-ridden by pilots in the field, as they eliminate the ability to train for required maneuvers, such as slow flight at high altitude, when there is no intention to land and the gear should not be down.
The invention, through much richer monitoring of more aspects of aircraft condition, allows a better, more accurate, more useful system. Aspects of aircraft condition applicable to the proper time to put the gear down:
- If Altitude is not near the ground, aircraft is not landing, having gear down is generally not desirable, so monitoring Altitude Above Ground Level (AGL) is one indication to check gear.
- If you are not descending, you are not landing, so having a negative vertical speed is one indication to check gear.
- If you are at high cruise speed, you are not landing, so monitoring Airspeed in knots (KTS) is one indication to check gear.
- By monitoring and verifying if the green lights are on or the red lights are on the invention knows if the gear is currently down and locked or up.
The best case to verify that gear should be down is to combine all of this above into one rule set to know if the gear should be down or not. We have a functional prototype of the system for this use case. For the aircraft we are testing in (a 1979 Beech A36 for this function), we currently have set a “Check Landing Gear” audible alert to come on only when all 3 conditions are met:
- Altitude is less than 1200’ AGL
- Vertical Speed is less than -200 ft/min
- Airspeed is less than 120 kts.
- Monitoring of current gear position will be added at a later date.
As each of these conditions and condition limits for alert are adjustable to meet the requirements of any aircraft, this is far superior to anything on the market today.
SAFETY WARNING SYSTEM – STALL/SPIN – VIRTUAL CO-PILOT
A significant number of fatal accidents in general aviation aircraft are a stall and spin that occurs low to the ground when turning base to final to line up with a runway and land. This can be because of pilot distraction or from a tightening of the turn because the pilot overshot runway alignment due to poor technique or to wind blowing them further than anticipated into the turn. According to a study by the Air Safety Foundation of 450 stall spin accidents from 1993 to 2001, 80% of them started from an altitude of less than 1000’ AGL, which is the pattern/landing altitude at most airports. In a 1970’s study by NASA looking at altitude loss in spins of several aircraft, the Piper Arrow, a common general aviation aircraft, lost an average of 1160’ in a spin when flown by a professional test pilot. The average private pilot can be assumed to not do as well, these accidents are often fatal.
The typical aircraft has a stall indicator that works by sounding an alarm when a wing stalls and has an airspeed indication for stall speed in various configurations (flaps down or flaps up). The issue with that is that stall speed is dependent on several factors that are not taken into account of by the Airspeed Indicator. One of these factors is bank angle. When a wing is banked 45°, stall speed increases by 20%, when banked 60°, stall speed increases by 40%. As speed is already decreased to prepare for landing at this point, the more the pilot tries to tighten the turn to final, the more likely they are to stall.
The invention can help solve this problem through rule sets and by telling the pilot what action to take, rather than just what problem is occurring. Using the Beech A36 for the example, rule set might include:
- Altitude below 1500’ AGL
- Airspeed below 120 kts
- Aircraft Bank Angle over 30°
- Gear is down (if retractable)
- Could either sound an alert or instruct pilot to reduce bank angle to avoid a stall/spin.
COMPANY OR ORGANIZATION OPERATIONS AND/OR SAFETY COMPLIANCE MONITORING AND LOGGING – VIRTUAL BOSS
Many aircraft are owned by organizations such as companies, flying clubs or flight schools. As operator representatives do not often fly along on most flights, it is an “honor system” to verify that the pilot is actually operating the aircraft in a safe, mechanically sound, per company/club/school procedures.
For example, aircraft engines need to be rebuilt, typically every 2000 hours of operation or so. How the engine is operated has a very large impact on how long it will last. For example, operating at 75% power vs. 65% power will significantly reduce engine life, and increase operating expenses. As aircraft operate at very different altitudes, with associated different air densities, correctly setting the power depends on several variables. A typical operator policy would be to not operate the engine in cruise at more than 65% power, regardless of altitude.
Below is the power setting table for a Lycoming O-320 engine:
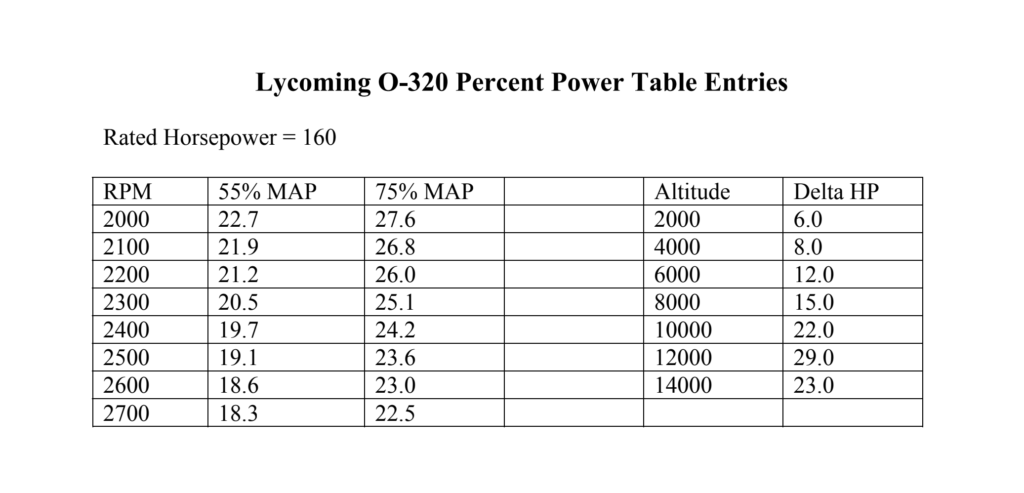
This invention helps operators verify proper operation of their aircraft by several means, including:
- Recommending proper setting for RPM and Manifold Pressure (MP) to set for the desired altitude and power setting for cruise flight when a cruise aircraft condition occurs
- Recommending a change in power setting when altitude changes and a cruise aircraft condition occurs
- Logging actual operation to verify it complies with operator rules.
Another related example is that if the proper RPM and MP are set, as well as the fuel / air mixture is properly leaned, that should result in an acceptable Exhaust Gas Temperature (EGT) and Cylinder Head Temperature (CHT) of the engine. This invention can monitor the EGT and CHT of each cylinder, and if an abnormal condition occurs, instruct the pilot what to change, such as leaning or enrichening the mixture control
TRAINING STEP BY STEP COACH, RECOMMEND AND MONITOR – VIRTUAL CFI
Pilot training is an expensive and laborious task. It is not unusual for someone training to be an Airline Transport Pilot (ATP) to spend over $100,000 to complete the required training. This invention can be used to standardize in-air or in-simulator training syllabus and methods, saving significant costs for the training operator and saving time and cost for the trainee.
This is accomplished by programming sequential aircraft conditions and rule sets for each maneuver to be trained. For example, one required training maneuver is the Power Off Stall. The manual steps required of the pilot to successfully accomplish a Power Off Stall in a Piper Archer aircraft are:
- This entire maneuver is required to be accomplished at a minimum altitude of 1500’AGL
- Establish straight and level flight on a cardinal heading (North, South, East of West) at cruise speed of 105 kts
- Perform a clearing turn, either a 180° turn or 2 90° turns without changing altitude more than 100’
- Reduce power to idle
- Use the control yoke to maintain elevation in order to slow down
- Once down to Vy speed = 76 kts (best climb), put the nose down to maintain that speed and add power to 1300 – 1400 RPM
- Upon reaching the desired stall altitude, reduce power to idle, hold altitude with the control yoke by continually increasing pitch attitude until the stall alert goes off
- Recover from the stall with minimal altitude loss by adding full power and slightly reducing the pitch attitude.
For training / learning purposes, each of these steps could be programmed into a rule set and presented, audibly, visually or otherwise to the student pilot flying with a Certified Flight Instructor (CFI). This would greatly reduce work load on the instructor, as they are responsible not only for talking the student through each step of the maneuver, but also looking outside the aircraft for traffic avoidance, and monitoring/correcting the student’s actions. In addition, since prompting will be consistent for each trial of the maneuver, training time will be reduced and nothing will be missed due to distractions of the CFI due to other concurrent duties.
TRAINING PROGRESS MONITORING AND LOGGING – VIRTUAL CFI
In the training scenario for Power Off Stall mentioned above, in order to pass a pilot Practical Test, each portion of each maneuver must be performed to FAA stated minimal criteria. When a student is first learning, the number of things to pay attention to simultaneously, such as Airspeed, Pitch Attitude, Gear and Flap position and more are extremely overwhelming, so training often starts with the student pilot controlling fewer variables, such as the control yoke, and the CFI controlling other variables, such as throttle settings. As the student progresses in abilities, his workload is increased.
This invention can be used to track and log progress. For example, as the student continues taking lessons, do they progress from being able to hold altitude within 300’ to within 200’. Each flight performance can be logged. Then, the maneuver rule set can be changed both standardize when the student is ready to have additional workload added, and the standard limits for “success” in the maneuver can be tightened. This is analogous to current video games, where level 1 is easier and as the user skill set increases, each additional level gets harder until the student has mastered the maneuver.
TRAINING PROGRESS – SOLO VIRTUAL COPILOT
Once a student pilot has reached the stage where they can demonstrate maneuvers in a safe manner, but not yet to the standards of a certificated private pilot, they are allowed to take an aircraft by themselves (solo) in order to practice to increase proficiency until they are ready to demonstrate full proficiency to an instructor, who will then sign them off to take the Practical Test with an FAA Designated Examiner.
This invention can be used as a sophisticated, automated monitor, much like the OnBoard Diagnostics (OBD) in a car that is now sometimes tied to a logging device for auto insurance. In this case, the rules set would match the FAA Airman Certification Standard (ACS) requirements for each maneuver. Again using the Power Off Stall example from above, the ACS standards for a Private Pilot Practical Test are reprinted below:
The combination of these requirements could be incorporated into a rule set, with warnings or alerts when they are exceeded, as well as recommended actions to improve performance in near real time, for example if the aircraft deviated more than 7° from the desired heading, a “turn right 7°” recommendation could be given. This near real time feedback would be instrumental in significantly reducing training time and cost.
TRAINING ACCOMPLISHMENT TESTING – VIRTUAL DPE
In the training scenario for Power Off Stall mentioned above, in order to pass a pilot Practical Test, each portion of each maneuver must be performed to FAA stated minimal criteria. For example, for the Private Pilot certificate, the general criteria are that the pilot must maintain heading with 10°, altitude within +- 100’, bank angle within +-10°. For airspeed, for most maneuvers, the requirement is +-10 kts, but when landing, it is -0, +10 kts, as getting slow on landing can lead to that stall/spin.
Most student pilots train with one instructor until that instructor feels they are ready to take the Practical Test. Many flight schools then have the student fly with another instructor to verify proficiency, as well as review training from the primary instructor. This invention would allow that step to be skipped entirely, as the logs of the student’s solo practice flights could be used to fully demonstrate proficiency for all required maneuvers. The student will know before they take the test that they meet FAA requirements, and are highly likely to pass the Practical Test.